801-859-1523
RILEY REYNOLDS
MECHANICAL ENGINEER
![]() | ![]() | ![]() |
---|---|---|
![]() |

ABOUT ME
I am a goal-oriented mechanical engineer who is passionate about improving healthcare through high-tech and high-quality devices. I am an honest self-starter who knows that no matter who signs my paycheck, I am self-employed. I am a team player who thrives when working with healthcare professionals to help drive product design. I am organized and proactive which helps me have a sharp focus on product and company vision. Most importantly, I am a life-long learner.
MULTI-PATIENT VENTILATION
​To help the world cope with the COVID-19 pandemic, I worked with several researchers, physicians, and respiratory therapists to develop and validate a method for multi-patient mechanical ventilation. We completed a total of four experiments with two human sized pigs: one healthy and one with lipopolysaccharide (LPS) induced acute respiratory distress syndrome (ARDS).
​
With the addition of a needle valve on each animal's inspiratory limb, we successfully oxygenated both animals.
​
Here is a link to a video with more information about the studies:
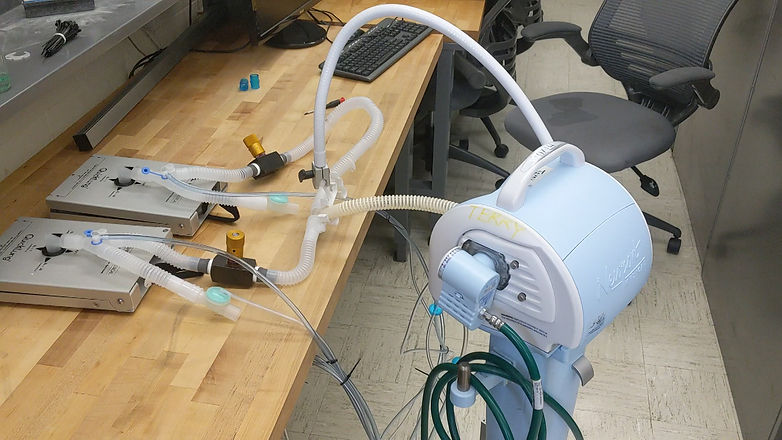
CATHETER PLACEMENT DEVICE
Within the Terry Research Lab at UNL, I led a team of researchers and physicians to develop a device for placing a catheter into the peritoneal cavity. Unlike devices currently on the market, our device simplifies the process to a point where it can be used by a field medic on the battlefield.
​
As part of the development of the new device, we experimentally determined the preperitoneal and peritoneal insufflation pressures in human-sized pigs. Using the knowledge of these pressures, we created a device that successfully accesses the peritoneal cavity with minimal training.

​
ULTRADENT PRODUCTS
​While working at Ultradent as an R&D Engineering Technician, I led a team of engineers and industrial designers to design new dual barrel syringes. The designs were modeled in SOLIDWORKS and prototyped using Connex and FormLabs 3D-Printers. The new syringe design was more ergonomic and decreased chemical waste by 26%.
​
I also worked with a team of automation engineers to develop a semi-automated machine capable of filling the new syringes. The design included a positive displacement pump and was capable of filling both dual and single barrel syringes. We were able to increase syringe filling rate by nearly 400% while maintaining ± 0.5% fill accuracy.​
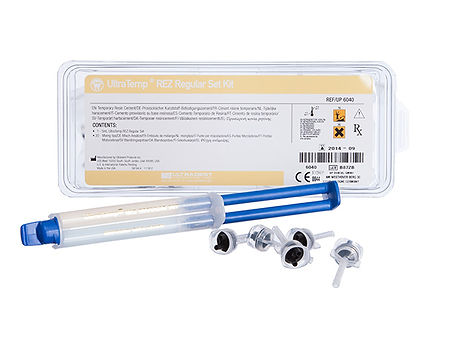

BYU MARS ROVER
For my senior design project at BYU, I participated in the University Rover Challenge (URC) in Hanksville, Utah. The first semester on the project, I worked on a team to design and manufacture a new rocker-bogie chassis. With the new design, we increased the tipping angle from 40 degrees to 65 degrees and significantly increased the stability.
​
After completion of the chassis, I was selected to be the team lead for the second semester as well as for the competition. In the end, we placed 10th in the competition.
​
Here is a link a video we submitted as part of the competition: https://www.youtube.com/watch?v=kN6pC5qmFv8&t=1s
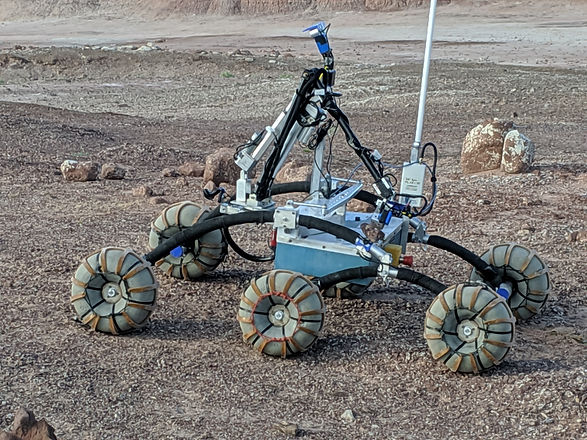

BYU JUMP COUNTER
While at BYU, I worked with a team of researchers to create a MATLAB algorithm to assist figure skaters during training. Using an IMU, the algorithm counted jumps, calculated jump height, and measured peak rotation speed. A more in-depth summary of the project can be found here: https://journals.plos.org/plosone/article?id=10.1371/journal.pone.0206162
​
I also worked on a project to create a device that can accurately measure the peak force figure skaters experience while performing. We attached strain gauges to each stanchion to directly measure the force. With the new device, we were able to measure the peak force within 3% error.
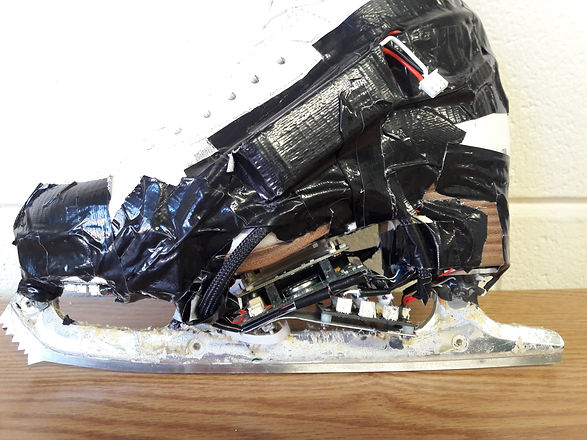


BRIGHAM YOUNG UNIVERSITY

UNIVERSITY OF NEBRASKA - LINCOLN

ULTRADENT PRODUCTS INC.
